Seems like every year somebody makes something cool out of bamboo: bicycles, snowboards, laptops, or a thousand other things. But the most common apps we see are slightly more mundane--flooring and cutting boards. Which got us wondering, how the heck do they get that stalk-like plant into flat, laminated boards?
People are still figuring out new ways to board-ify bamboo--here's a patent application for a rather complicated new method, for true production method geeks--but we think we've found the most common way it's done. Click the link below and read on.
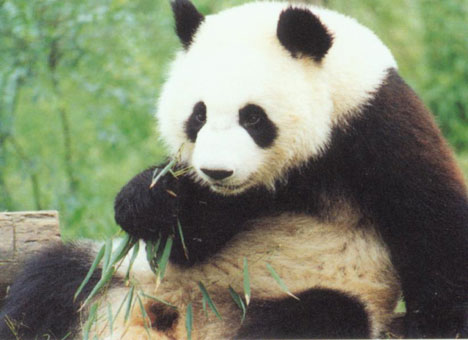
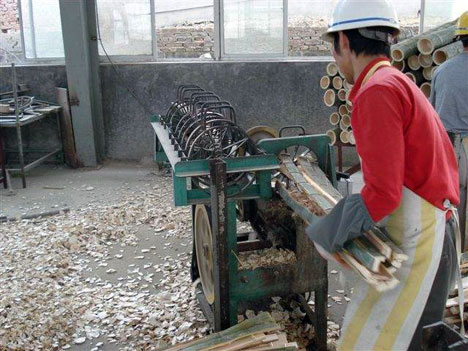
First, they harvest the bamboo by capturing Panda bears and evacuating their stomachs. Sorry, just kidding. First they harvest the bamboo, which can be done manually with machetes, knives and saws, but which is probably done on an industrial scale using farm equipment. (Our research indicates John Deere does not make a Bamboo Harvester, but if anyone's got a pic or a link...) Also, we're talking about the big kind of bamboo, not the skinny kind they once used for fishing poles; you've probably seen the wide-diameter poles in an old kung fu movie.
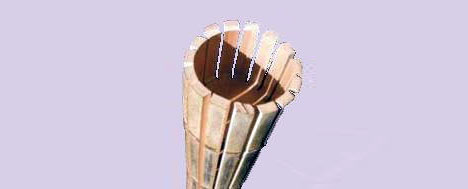
Secondly, they cut the stuff into strips, lengthwise. (Our source could not confirm this, but we believe they then spend the next three days defending the factory against rabid, invading Pandas that smell bamboo blood.)
After being cut into strips the bamboo is pressure-steamed, a process also called carbonization, to get rid of bugs. The longer you carbonize the bamboo, the darker--and softer--it gets, meaning it's only done up to a point.
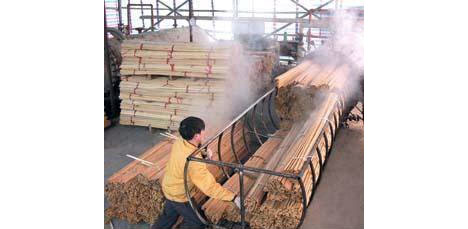
Now "purified," the bamboo is inspected and sorted into grades. Following that it's kiln-dried to remove moisture, and afterwards it's milled into nice, uniform strips.
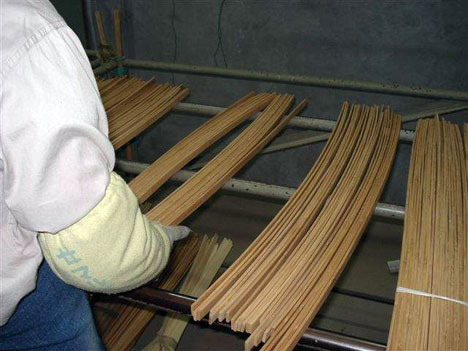
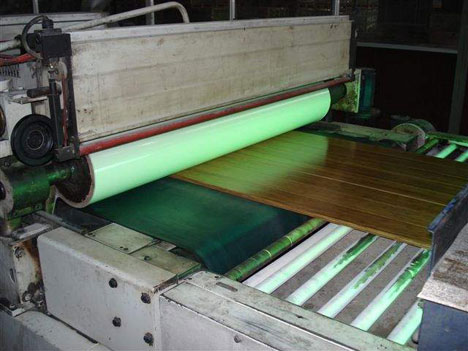
Next, the strips are laminated into sheets or blocks using a combination of glue, heat, and/or UV. (It is deemed ready when even the angriest Panda cannot separate the strips.)
Finally, the laminated sheets or blocks are further machined into their end product.
Post time: Jan-09-2023